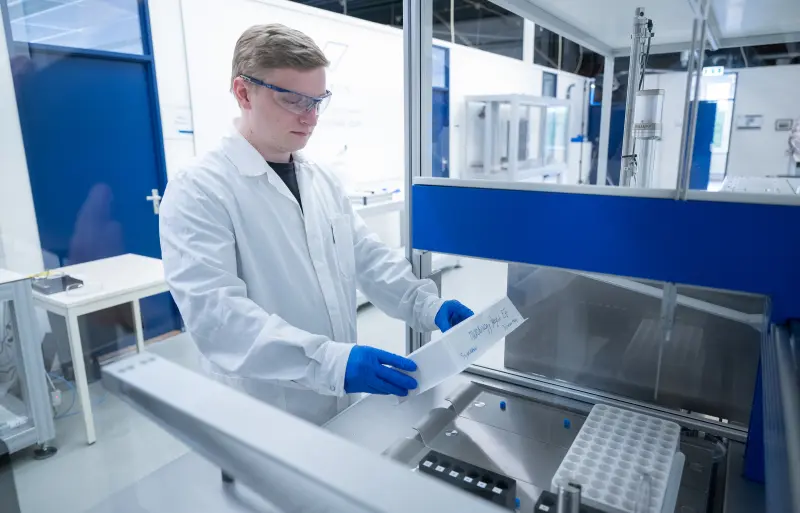
Unleashing Efficiency and Precision
Tailored Solutions for Your Lab Automation Needs
At Synchron, we offer an extensive range of innovative solutions to meet your specific requirements. Our open and flexible state-of-the-art XYZ liquid handlers, integrated solutions, and custom lab instruments are built to your exact specifications.
We provide comprehensive services including advice and design for systems and software architecture. Additionally, we assist in the setup of your workflow/method, perform data interface programming, develop custom user interfaces, conduct instrument validation at the factory (FAT) and on-site (SAT), and offer dedicated service and support, along with application assistance.
With our multidisciplinary engineering capability, diverse application knowledge, and successful collaborations with leading laboratories and startups, we deliver results that exceed expectations.